1. In 2012 Labboun Rafic Mohammed (Muslim
cleric) with alleged links to Hezbollah was arrested in Merida Mexico.
He was also a fugitive from U.S. justice.
2. He arrived in Yucatan and apparently
used a network of Lebanese government officials. These officials
colluded with parties in Belize who provided a fake passport from
Belize.
3. Labboun’s fake passport was in the name
of Wilhelm Dyck. Dyck was a deceased Mennonite child. Labboun also
possessed a drivers license in the same name.
4. Razur Antonio Elias – Director
of the Mexican Drug Observatory indicated in a report that Islamist
organizations are linked to Mexican drug traffickers on the Yucatan Peninsula. Traffickers are providing passports, birth certificates, and drivers licenses from Belize. COST REPORTED $25,000.
5. The network is also providing transfers of Hezbollah members with forged paperwork to pass through Mexico to the United States. Merida Mexico appears to be the Nexus of this operation.
More at channel5belize.com, Who helped Hezbollah terrorist get Belizean passport and IDs?
We have been able to establish that that
very same day, a person posing to be Wilhelm Dyck made an application
for a Belizean passport at the Passport Office in Belize City; that’s on
the twenty-ninth of August, 2012 and that he paid a hundred dollars to
expedite the process for the express issuance of the passport. And we’ve
also been able to establish that the following day, a passport was
indeed issued; that is the thirtieth of August, 2012, in the name of
Wilhelm Dyck.
…
“The information in the computer also had a
photograph of the person purporting to e Wilhelm Dyck. And immediately
upon pulling up the photograph, the senior immigration officer without
any prompting from the police authorities said that that person looks
like a Lebanese national. Which raised the question; which has to be
asked to the relevant persons who accepted the application and processed
the application: if there weren’t some alarms that went off in their
head when they saw a person looking like he did appearing before them
claiming to be Wilhelm Dyck. As you know, when you now apply for a
passport, you have to physically go to the office and have your photo be
taken. In the past, there was system where you would bring a photograph
already taken, the J.P. would just sign the photograph and the birth
certificate and would certify you as being the person who appears on the
photograph and someone who they have known for a period of time. This
instance, there is a Justice of the Peace that has now been detained and
is being interviewed by police authorities. That person incidentally
was the same person who had their home burnt down over the holidays and
so she could not be immediately found yesterday. She has since been
found and is now being interviewed.”
That was several months ago. No news since on what appears to be infiltration in Belize.Related: California Muslim Arrested in Mexican Hezbollah Bust
‘Magical’ printers produce clothes, medical devices
Meet the Israeli-American company behind the amazing 3D printing technology that allows a disabled little girl to move her arms.
By Abigail Klein Leichman February 25, 2013, No Comments
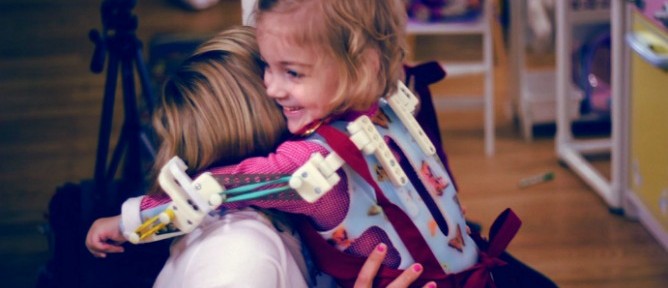
Emma using her Magic Arms printer-made exoskeleton.
“It does seem like magic,” says Joe Hiemenz, spokesman for 3D printer manufacturer Stratasys, which has dual headquarters in Minneapolis and Rehovot, Israel.
Spread the Word
• Email this article to friends or colleagues
• Share this article on Facebook or Twitter
• Write about and link to this article on your blog
• Local relevancy? Send this article to your local press
Indeed it was magical when preschooler Emma Lavelle was able to use
her arms for the first time with the help of a custom-designed robotic
exoskeleton made with a Stratasys Dimension 3D printer – so magical that
the device has been nicknamed “Magic Arms.”• Email this article to friends or colleagues
• Share this article on Facebook or Twitter
• Write about and link to this article on your blog
• Local relevancy? Send this article to your local press
The little girl has a congenital disorder that compromises her joint mobility and muscles. Researchers at the Nemours/Alfred I. duPont Hospital for Children in Philadelphia knew of a metal exoskeleton for adults suffering similar conditions, but it was too big and heavy for a child.
The Stratasys printer enabled them to fashion a lightweight alternative that has been nominated for the Designs of the Year 2013 awards by London’s Design Museum. And in his February 12 State of the Union address, US President Obama announced that “3-D printing … has the potential to revolutionize the way we make almost everything.”
“It works identical to an inkjet printer — forming a product layer by layer, but making it from some kind of plastic or resin,” Hiemenz tells ISRAEL21c.
“A head puts down the material in very thin layers following a tool path created by a CAD [computer-assisted design] file, so whatever you have designed through CAD is going to come out. In the case of Magic Arm, it was plastic coming out of the printer in molten form.” This is the same sturdy plastic used in LEGO bricks.
‘Tech couture’
US-based Stratasys and Israel-based Objet – both leading manufacturers in the 3D printing field – merged in 2012. The line of printers assembled in Israel retains the Objet brand name, marketing VP Arita Mattsoff tells ISRAEL21c.
At Paris Fashion Week in January, Dutch designer Iris van Herpen unveiled two ensembles from her new haute couture collection that were made with an Objet Connex multi-material 3D printer.
Massachusetts Institute of Technology Prof. Neri Oxman, who was born in Israel, produced the intricate printed outfits in collaboration with Austrian architect Julia Koerner, a lecturer at UCLA-Los Angeles, and Belgian software developer Materialise.
The designer had sought out Oxman after seeing her 3D-printed “Imaginary Beings: Mythologies of the Not Yet” display last spring in Paris.
“The Connex line has unique abilities to print different material qualities simultaneously,” says Mattsoff.
“The van Herpen skirt and dress have a combination of rigid and flexible parts made of three different material properties. You could not make this dress without the Connex technology. It allows you to really attempt new things in a unique way.”
Oxman said, “The incredible possibilities afforded by these new technologies allowed us to reinterpret the tradition of couture as ‘tech couture,’ where delicate handmade embroidery and needlework is replaced by code.”
Van Herpen told Fashion Week reporters that she believes “it will only be a matter of time before we see the clothing we wear today produced with this technology, and because it’s such a different way of manufacturing, adding layer-by-layer, it will be a great source of inspiration for new ideas.”
Endless possibilities
Those new ideas are not limited to fashion or even to medical and dental devices.
“This industry started about 25 years ago to make prototypes mainly for the aerospace and automobile industries, and other high-end applications that have deep pockets to explore new technologies,” says Hiemenz. “They’re not prototypes anymore; they’re real products now.”
The medical applications are among the most dazzling, he adds. The 3D printing process has been used to make custom orthotics for disabled American veterans, a better device to treat clubbed feet and even a sophisticated heart surgery tool. The process allows for creating complex interior passages inside devices to carry air or liquids.
Design News magazine recently named Stratasys a Golden Mousetrap awards finalist for its Mojo 3D Printer, its Objet30 3D Printer, and its Objet line of digital materials. The Objet product line won the 2012 Leadership in Engineering Program from US publication Design World, and the Objet260 Connex received an innovation award from Dental Advisor magazine.
Hiemenz says that the news about Magic Arms has resulted in a flood of inquiries from parents hoping that the printed exoskeleton could help their child, too. A foundation is being set up for this purpose at the initiative of Eric Jenson, who produced a video showing Emma and her Magic Arms. The goal is to make 50 of these exoskeletons per month, perhaps giving them free to disabled children in developing nations.
1 comment:
maybe it was a certain antisemitic anti-US "African Arabian" fr San Antonio
Post a Comment